How to Debug Your Process Control System in 8 Steps
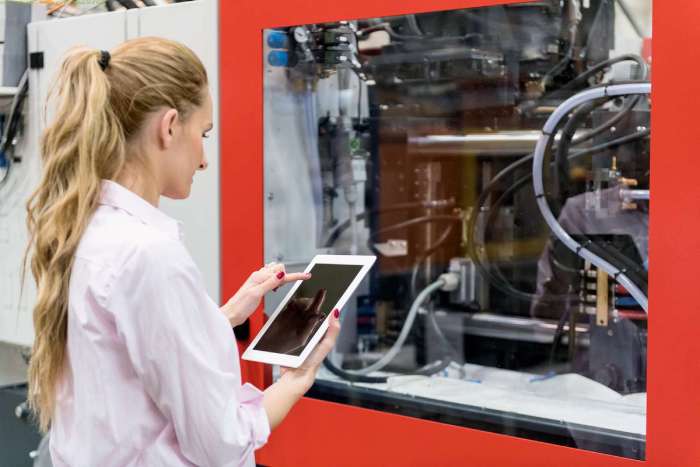
How to Debug Your Process Control System in 8 Steps
To assist you in locating and debugging your process control system with Industrial automation, which may be built and utilized over time, we’ve merged this eight-step technique from this month’s issue of Plant Engineering. By starting with little more than a pencil and piece of paper and utilizing specific readily available tools, you may achieve the proper concentration on a particular system or process.
Table of Contents
1. Lay down the steps.
First, create a graph of the intrigued system and its primary shapes. Even if you might eventually want to use a drawing program like Visio, a “back of the envelope” diagram outlining the primary system operations will do for the time being.
2. Identify crucial elements
Next, make a note of each process’ crucial elements. The essential components may vary depending on the business, but for many industrial processes, you should consider items like motors, variable frequency drives, sensors, and power supplies.
3. Assign metrics to important parts
For each of the imperative components you listed in the previous phase, choose some “operational metrics.” You can measure these to get critical information about the component’s performance.
Great candidates for metrics include data about a component that can be roughly measured and for which information can be gathered at a single moment (for instance, meter estimations, waveform captures, observations, and photos). Obtain important numerical data (like a temperature reading) or evocative data (such as waveform shape from a variable speed drive).
4. Take the dimensions
It is essential to monitor and keep track of the critical component metrics. The procedure of gathering this data can be easy. Although starting with a pencil and paper is possible, you will eventually want to record and examine component metrics in a spreadsheet or database.
Here are some simple “rules of thumb” for taking accurate and practical measures. Your experience and expertise are the best resources for deciding what to measure and how to measure it. Track the current as it flows after starting your measurement at the power source.
5. Create an information “dashboard.”
Despite the possibility that statistical data, like the one you acquired in Step 4,
might be a valuable tool for analysis and forecasting, translating rows and columns of unprocessed data can be difficult. To deal with this kind of data overload, an effective technique is to decide in advance what range
of values each metric defines as OK, suspect, severe, and excessive.
Create a straightforward, color-coded status for each system component using data ranges,
which you can then show on a spreadsheet, whiteboard, or notepad. The resulting simplified, high-level perspective of the system,
free of distracting detail, may be used to facilitate data analysis and decision-making for complex systems.
6. Set components’ priorities for care, upkeep, and spending
Now that you have a clean, uncluttered picture of the condition of each component of the system, you can decide which ones need your attention first.
7. Make a choice.
Choose what to do next for each item on your list of priorities: Does it need to be repaired (for example, the conveyor’s motor resized to handle the load demand better)? Is it in need of replacement? Should I keep an eye on it?
Another option is to let it fail without making preparations or committing any money or resources. The decision-making process can be significantly aided by objective data on essential factors that have been ranked.
8. Improve and broaden, but maintain flexibility
Once you’ve put a winning approach in place, you may keep enhancing and expanding it. Be sure to maintain mental flexibility as your system approach changes. If you gather data using a variety of all-purpose, portable instruments, your system approach will be flexible enough to evolve when processes, components, priorities, and your needs change.
Consider asking yourself whether your approach will be improved by adding new processes or components and whether using other metrics would do so. Do you need to invest additional money in new tools, training, or staff to carry out the strategy effectively? Should your system diagram be better provided or more detailed? Do you want to invest money in programs, databases, or spreadsheets that are more efficient at analysis and storage?
An approach for the long term
When plant managers have a precise, understandable, and controlled grasp of a system’s fundamental operations and critical elements, they may better use their finite resources, including time, money, equipment, and employees. You might also support labor expansion, equipment acquisitions, and process improvements with the complex data you get.
The time and effort required to develop and manage a successful system strategy will pay off in wise decisions, time and money savings, and the peace of mind that comes from understanding where you are now and where you’re headed. This is true whether you begin small and keep it straightforward or go right in and create a thorough approach with several controlled metrics.